Are you curious about how acrylic is made? Acrylic is known as polymethyl methacrylate (PMMA), a very popular material used in a wide range of applications such as medical devices to consumer products. The versatility, transparency, and strength of acrylic material have made it an increasingly popular choice in modern times.
In the polymerization process, MMA and MA are combined with a polymerization initiator, such as benzoyl peroxide, to start the reaction. The initiator breaks down into free radicals, which react with the monomers to form a long chain of repeating units, called a polymer. This polymer is then processed into the final acrylic product, such as sheets, rods, or fibers.
In this blog, I will highlight into the science behind acrylic and explore the process of how it is made. I will also touch on its properties, and uses. So, whether you’re an engineer, designer, or simply a very curious individual, this blog is sure to satisfy your curiosity about acrylic. So, let’s get started!
Related Reading
- Benefits of Cast Acrylic
- Cast Vs Extruded Acrylic
- Top 10 Best Acrylic Fish Tanks in 2023
- Sublimation on Acrylic for Beginners
Raw Materials for Making Acrylic
Acrylic is made from a polymer called polymethyl methacrylate (PMMA), which is derived from a monomer called methyl methacrylate (MMA). The primary raw materials used to produce MMA are;
- Methyl Methacrylate (MMA): Methyl methacrylate is the primary raw material used to produce PMMA.
- Initiator: An initiator is used to initiate the polymerization reaction and convert the MMA monomers into PMMA polymer chains. Common initiators include organic peroxides, such as benzoyl peroxide and lauryl peroxide.
- Stabilizer: A stabilizer must be added to prevent thermal degradation and yellowing of the PMMA polymer. Antioxidants, such as hindered phenols, are commonly used as stabilizers.
- Processing Aid: Processing aids, such as polyethylene glycol and stearic acid, are also added to improve the flow properties of the polymer during processing and to reduce surface defects.
- Pigments and Fillers: Pigments and fillers can be added to modify the color and improve the mechanical properties of the PMMA polymer. Common fillers include glass fibers, calcium carbonate, and talc.
Note: In addition to these primary raw materials, various additives can be added to improve the performance and processing of the PMMA polymer. These include UV stabilizers, flame retardants, and antistatic agents, among others.
How Is Acrylic Made Step by Step?


Here is a step-by-step overview of the process:
Step 1: Monomer Preparation
The monomer preparation step in the manufacturing of acrylic involves mixing two main monomers: methyl methacrylate (MMA) and methyl acrylate (MA). The ratio of MMA to MA in the monomer mixture is important as it affects the final properties of the acrylic product.
The monomers are typically mixed in a reactor vessel along with a small amount of a stabilizer to help prevent polymerization during the mixing process. The mixture is then heated to a specified temperature to ensure a homogeneous blend. Once the monomer mixture has been prepared, it is ready for the polymerization step.
Note: It’s important to note that both MMA and MA are highly flammable and toxic materials, so proper safety measures and handling procedures must be followed during the monomer preparation step.
Step 2: The Polymerization Process
The next step is polymerization. This is the process of converting the monomer mixture of methyl methacrylate (MMA) and methyl acrylate (MA) into a polymer chain. The polymerization reaction is initiated by adding a polymerization initiator, such as benzoyl peroxide, to the monomer mixture.
When the initiator is added, it breaks down into free complete radicals, which initiate the polymerization reaction by reacting with the monomers to form a long chain of repeating units, called a polymer.
The polymerization reaction is exothermic, which means that it generates heat, so the reaction is usually carried out under controlled temperature and pressure conditions.
The polymerization reaction takes place in a reactor vessel where the reaction time, temperature, and pressure are carefully controlled to produce a polymer with the desired properties.
The polymerization reaction can be carried out using either batch or continuous processing techniques, depending on the specific needs of the manufacturer.
Once the polymerization reaction is complete, the mixture of polymer and residual monomer is subjected to purification to remove any residual monomer and other impurities.
Step 3: Purification
The purification of acrylic is quiet easy as it involves removing
any residual monomer and other impurities from the mixture of polymer and residual monomer produced during the polymerization step. This is very important to ensure that the final product has the desired properties and performance for use.
The purification process typically involves a number of steps, including;
- Degassing: The mixture of polymer and residual monomer is purged with nitrogen to remove any residual monomer and other volatile impurities.
- Dissolving: Next, it is dissolved in a solvent, such as toluene or acetone, to further remove impurities and improve the clarity of the polymer.
- Precipitation: The polymer is then precipitated out of solution by adding a non-solvent, such as methanol or ethanol to form a solid that can be easily separated from the solvent.
- Drying: The precipitated polymer is dried to remove any residual solvent.
- Pelletizing: The dried polymer is then formed into pellets, which are a convenient form for further processing into the final product.
Step 4: Final Product Formation
The final product formation step in the manufacturing of acrylic involves converting the purified polymer into the desired final product. There are several processing techniques that can be used to form the final product, including:
- Casting: This is when the polymer is poured into a mold, where it solidifies to form a solid sheet or rod. This method is often used to produce large, flat sheets or solid rods with consistent dimensions.
- Extrusion: Extrusion happens when the polymer is melted and forced through a die to form a continuous sheet, rod, or fiber. This method is often used to produce shapes with a consistent cross-section.
- Injection Molding: During this step, the polymer is melted and injected into a mold, where it solidifies to form a solid part with a complex shape. This method is often used to produce intricate parts with a high level of dimensional accuracy.
The product can then be formed into sheets, rods, fibers, or other shapes as required. After the final product has been formed, it may be subjected to further processing, such as cutting, grinding, polishing, or UV protection treatment, to enhance its properties and appearance. The final product is then ready for shipment and use.
Types of Acrylic
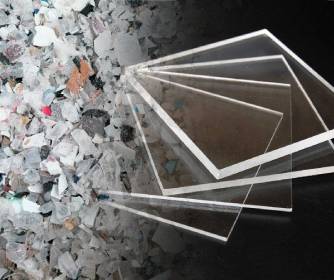
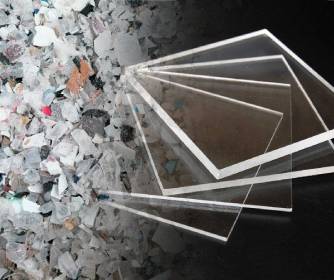
Acrylic, also known as polymethyl methacrylate (PMMA), is a versatile polymer that can be manufactured in a variety of forms with different properties to suit different applications. Some of the most common types of acrylic include:
- Extruded Acrylic: Extruded acrylic is a transparent plastic sheet that is manufactured by heating the polymer and forcing it through a die. This type of acrylic is often used in applications where clarity, stability, and affordability are important, such as in windows, skylights, and sign boards.
- Cast Acrylic: Cast acrylic is a transparent plastic sheet that is manufactured by pouring the polymer into a mold and allowing it to solidify. Cast acrylic is known for its high optical clarity, impact resistance, and weather resistance, making it a popular choice for applications such as aquariums, displays, and signage. Here are the benefits of cast acrylic
- Acrylic Block: Acrylic block is a solid, opaque plastic that is often used as a substitute for glass or metal in applications that require a high degree of durability, such as in machine parts or structural components.
- Acrylic Rods and Tubes: Acrylic rods and tubes are cylindrical shapes made from the polymer, and they are often used in applications that require a strong, transparent material, such as in laboratory equipment or lighting fixtures.
- Acrylic Resin: Acrylic resin is a liquid form of the polymer that can be used as a binder, coating, or adhesive in a variety of applications, such as in paints, coatings, and adhesives.
Related Post: Cast Vs Extruded Acrylic
Recommended Product: Langaelex 10 Pieces 5’’ x 7’’ x 0.043’’ (Actual Thickness 1.0mm -1.2mm) Acrylic Sheets Clear Extruded Plexiglass for Picture Frame Glass Replacement, Projects Display, Painting
Initiators and Stabilizers in Acrylic Production
Initiators and stabilizers are crucial components in the production process of acrylics. Initiators are used to initiate the polymerization reaction that converts the monomers into a polymer, while stabilizers are used to prevent thermal degradation and yellowing of the polymer over time. Common initiators used in acrylic production include organic peroxides, while antioxidants such as hindered phenols are commonly used as stabilizers.
Processing Aids for Acrylic
Processing aids are chemical additives that improve the flow properties of the acrylic during processing and reduce surface defects. They are used to enhance the processability of the material and improve its appearance. Examples of processing aids used in acrylic production include polyethylene glycol and stearic acid.
Pigments and Fillers Used in Acrylic Production
Pigments and fillers are added to acrylic to modify its color and improve its mechanical properties. Fillers are used to enhance the strength and rigidity of the material, while pigments are used to add color. Common fillers used in acrylic production include glass fibers, calcium carbonate, and talc.
Differences Between Cast and Extruded Acrylic Sheets
Cast and extruded acrylic sheets are two different types of acrylic sheets with different manufacturing processes and properties. Cast acrylic sheets are made by casting the liquid acrylic into a mold and allowing it to cool and harden, while extruded acrylic sheets are made by melting and extruding the acrylic through a die. Cast acrylic sheets have better optical clarity and are easier to shape, while extruded acrylic sheets have better surface finish and are more resistant to impact.
Environmental Considerations in Acrylic Production
Acrylic production can have both positive and negative environmental impacts. On one hand, acrylic is recyclable and can be made from recycled materials, which helps reduce waste and conserve resources. On the other hand, the production process for acrylic can be energy-intensive and can generate greenhouse gas emissions. Additionally, acrylic production can generate waste and pollution if not properly managed. To minimize the environmental impact of acrylic production, companies can adopt sustainable practices such as using renewable energy sources, reducing waste, and implementing recycling programs.
Uses of Acrylic
Acrylic can be used for a wide range of applications due to its unique properties. Here are some of the common uses of acrylic:
- Signage and displays: It is often used to make signs and displays due to its transparency, which allows for easy viewing of printed or engraved text and graphics. Acrylic signs and displays can be made in a variety of colors and shapes, and can be backlit for added visibility.
- Windows and skylights: Acrylic is used as an alternative to glass in many applications due to its impact resistance and lightweight properties. Acrylic windows and skylights are often used in aircraft, boats, and architectural applications.
- Lighting fixtures: As a popular material for lighting fixtures due to its light transmission properties, which allows for bright and even illumination, it can be shaped and molded into different forms, allowing for unique and creative designs.
- Furniture: It can also be used to make acrylic furniture that has gained popularity in recent years due to its modern and minimalist look. Furthermore, acrylic chairs, tables, and shelves are lightweight, durable, and easy to clean.
- Aquariums and terrariums: It has become a popular material for aquariums and terrariums due to its high clarity and impact resistance. Acrylic aquariums can be made in custom sizes and shapes, and are less likely to crack or shatter than glass aquariums.
- Automotive parts: It is also used in automotive applications such as headlights, taillights, and instrument panels due to its impact resistance and optical properties.
- Medical devices: Lastly, acrylic is used in medical devices such as dentures, hearing aids, and lenses due to its biocompatibility and optical clarity.
Frequently Asked Question
Is acrylic really plastic?
Acrylic is a type of plastic, Specifically, it is a thermoplastic material that is made from a polymer called polymethyl methacrylate (PMMA).
What are made out of acrylic
Acrylic is used in a wide variety of applications, including signs, displays, lighting fixtures, windows, furniture, and even automotive parts. It is also commonly used in the production of aquariums and other types of water tanks.
Difference between plastic and acrylic?
While acrylic is a type of plastic, it has several properties that distinguish it from other types of plastics. Acrylic is more transparent and has better optical clarity than many other plastics. It is also more impact-resistant than glass, making it a popular alternative for applications where safety is a concern. Additionally, acrylic is more resistant to weathering and aging than many other plastics.
Is acrylic material eco-friendly?
The environmental impact of acrylic production can vary depending on the specific manufacturing process and how the material is used and disposed of. While acrylic is recyclable and can be made from recycled materials, the production process for acrylic can be energy-intensive and can generate greenhouse gas emissions. Additionally, acrylic can release harmful fumes when burned. To minimize the environmental impact of acrylic, it is important to use sustainable practices in its production and disposal.
Thoughts
In conclusion, the production of acrylic involves a complex process that requires precise control of raw materials, temperatures, and reaction conditions. However, the resulting PMMA polymer is a versatile and durable material that has a wide range of applications in various industries. From signage and displays to furniture and medical devices, acrylic’s unique properties make it a top choice for designers, architects, and manufacturers